Revolutionizing Safety: How Unmanned Operations Are Transforming Toxic Chemical Environments
In the world of chemical manufacturing, safety has always been a primary concern, especially in environments where toxic, corrosive, and highly reactive chemicals are handled. For years, operators have been exposed to dangerous conditions, risking their lives to carry out critical processes in these hazardous settings. But today, a revolutionary change is taking place. The introduction of unmanned operations is transforming how chemical manufacturing companies approach safety and productivity in toxic environments.
12/19/20244 min read
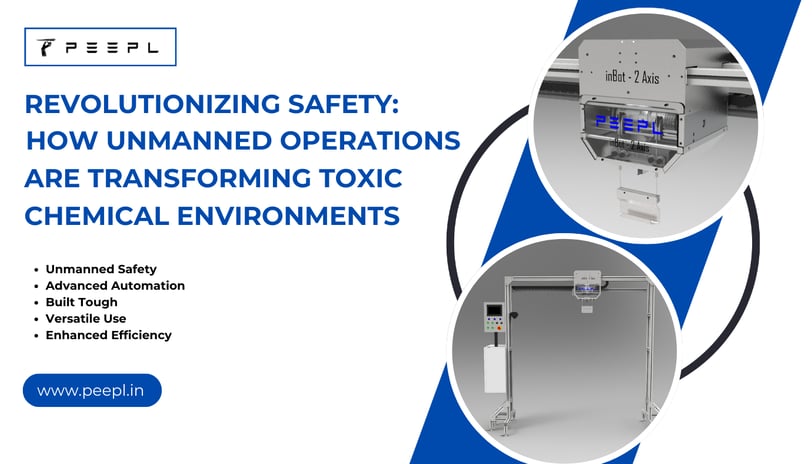
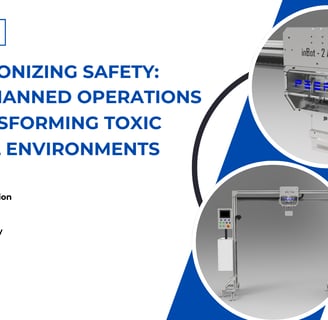
The Dangers of Traditional Chemical Manufacturing Operations
The chemical industry has long faced the challenge of balancing high efficiency with safety. In environments where chemicals react unpredictably or are highly corrosive, the stakes are incredibly high. Operators are required to manually interact with dangerous materials, whether it’s mixing chemicals, monitoring reactions, or performing maintenance. This constant exposure not only puts human lives at risk but also leads to significant downtime, equipment damage, and loss of productivity due to the corrosive nature of the chemicals involved.
The risks are not just theoretical; they are real and persistent. Chemical burns, inhalation of toxic fumes, and exposure to dangerous reactions can have catastrophic consequences. This danger, combined with the high cost of equipment repair or replacement due to corrosion, makes the need for safer alternatives even more urgent.
Introducing PEEPL Automation: Leading the Change in Unmanned Operations
At PEEPL Automation, we recognize the critical need for innovative solutions that ensure safety and efficiency in toxic environments. As a leader in industrial automation, we specialize in providing advanced robotic systems that are tailored to meet the specific needs of industries such as chemical manufacturing, pharmaceuticals, food, and packaging. Our solutions are designed to eliminate the risks associated with hazardous environments, ensuring that human operators are kept out of harm’s way while optimizing production processes.
One of our flagship products, the InBot 2 Axis and InBot 3 Axis robots, is revolutionizing how unmanned operations are implemented in high-risk chemical environments. These versatile robots are engineered to perform complex tasks with unparalleled precision, speed, and reliability, all while reducing the risk to human operators.
The InBot 2 Axis and InBot 3 Axis: Tailored for Toxic Environments
PEEPL Automation offers two variants of the InBot series — the 2 Axis and 3 Axis robots — both designed to work seamlessly in hazardous environments. The InBot 2 Axis is ideal for tasks that require high precision with two directional movements, while the InBot 3 Axis provides even greater flexibility, capable of handling more complex operations with three axes of movement. These robots are perfect for applications like palletizing, pick-and-place, material handling, and assembly in environments where safety is a top priority.
By deploying these unmanned robots in chemical manufacturing plants, companies can now automate processes that were previously carried out manually in dangerous conditions. Whether it's handling corrosive chemicals, performing inspections, or operating in highly reactive environments, the InBot robots ensure that all tasks are carried out with precision and without exposing workers to harmful substances.
Benefits of Unmanned Operations in Toxic Environments
Enhanced Worker Safety: The most immediate and obvious benefit is the improved safety of workers. By deploying unmanned systems, operators are no longer exposed to hazardous materials or dangerous reactions, significantly reducing the likelihood of chemical burns, inhalation injuries, and other health risks.
Improved Precision and Consistency: Unmanned systems are highly accurate and can carry out tasks with precision that is difficult for humans to achieve, particularly when dealing with volatile chemicals. These systems can maintain exact parameters, ensuring consistent and safe chemical reactions while minimizing human error.
Reduced Equipment Wear and Tear: The corrosive nature of chemicals can quickly degrade both machinery and the infrastructure of a manufacturing plant. Unmanned systems, designed to operate in harsh environments, are built with materials that withstand corrosion, reducing the need for frequent repairs and lowering maintenance costs.
Increased Efficiency and Productivity: Automated systems do not require breaks, can operate 24/7, and are capable of carrying out repetitive tasks more efficiently than human workers. This leads to higher production rates, reduced downtime, and improved overall productivity.
Cost Savings: By reducing the need for human intervention and minimizing downtime, unmanned systems lead to significant cost savings in labor, maintenance, and equipment replacement. Additionally, by ensuring that chemical processes are carried out with higher precision, these systems reduce waste and increase the yield of products, further driving down costs.
How PEEPL Automation Stands Out in the Industry
What sets PEEPL Automation apart is our commitment to delivering customized automation solutions that meet the unique needs of each customer. We understand that every manufacturing process is different, especially in hazardous environments, and we work closely with our clients to develop tailored solutions that maximize safety and efficiency.
Our InBot 2 Axis and InBot 3 Axis robots are designed with cutting-edge technology to handle the most challenging tasks in toxic chemical environments. These robots are not only built to endure the harsh conditions of chemical manufacturing but are also equipped with intuitive interfaces, making them easy to integrate into existing production lines. The flexibility of our robots allows them to adapt to various tasks, whether it's chemical handling, inspection, or assembly, providing unmatched versatility and reliability.
The Future of Unmanned Operations in Chemical Manufacturing
As technology continues to advance, unmanned systems in toxic chemical environments will only become more sophisticated. With machine learning,predictive analytics, the future of unmanned operations looks brighter than ever. At PEEPL Automation, we are committed to staying ahead of the curve by continuously innovating and enhancing our automation solutions to meet the evolving needs of the chemical manufacturing industry.
By implementing unmanned operations, chemical manufacturers can look forward to a safer, more efficient, and cost-effective future. With PEEPL Automation leading the way, the dream of a fully automated, risk-free chemical manufacturing environment is within reach.
Conclusion
Unmanned operations are transforming the chemical manufacturing industry, enhancing safety and productivity while reducing the risks associated with toxic environments. PEEPL Automation is proud to be at the forefront of this transformation, offering advanced automation solutions like the InBot 2 Axis and InBot 3 Axis robots to help companies streamline their processes and protect their workers. As the industry moves towards more automated and unmanned systems, PEEPL will continue to lead the charge in making manufacturing processes safer, more efficient, and more cost-effective for industries worldwide.